The Scientific Research Behind Porosity: A Comprehensive Guide for Welders and Fabricators
Understanding the complex devices behind porosity in welding is crucial for welders and producers aiming for impressive workmanship. From the composition of the base materials to the complexities of the welding process itself, a wide range of variables conspire to either worsen or relieve the visibility of porosity.
Understanding Porosity in Welding
FIRST SENTENCE:
Exam of porosity in welding discloses essential insights into the integrity and top quality of the weld joint. Porosity, identified by the visibility of tooth cavities or spaces within the weld metal, is a common concern in welding procedures. These spaces, if not correctly attended to, can endanger the architectural integrity and mechanical properties of the weld, bring about possible failures in the finished item.
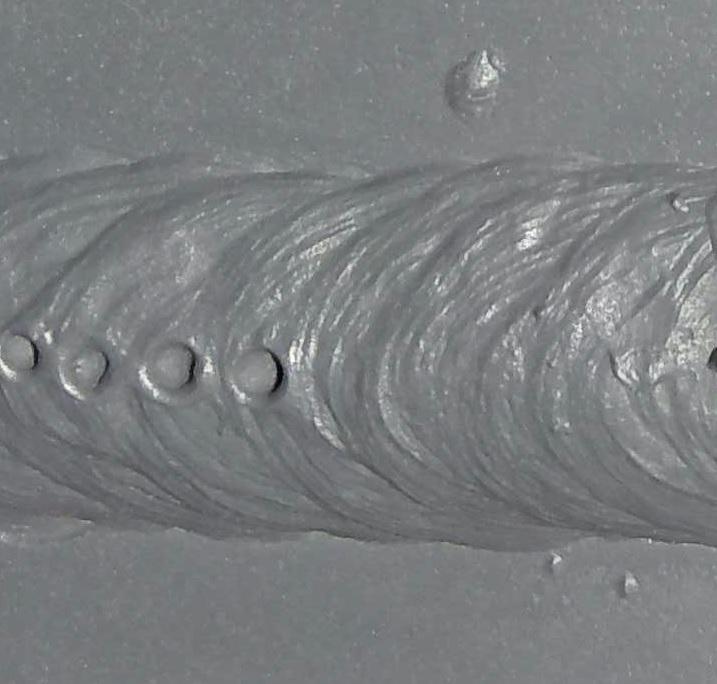
To discover and quantify porosity, non-destructive screening approaches such as ultrasonic testing or X-ray inspection are often used. These methods enable the recognition of inner problems without compromising the honesty of the weld. By examining the size, form, and distribution of porosity within a weld, welders can make informed choices to improve their welding procedures and accomplish sounder weld joints.

Factors Affecting Porosity Development
The incident of porosity in welding is influenced by a myriad of factors, ranging from gas securing effectiveness to the intricacies of welding parameter setups. One vital element contributing to porosity development is inadequate gas securing. When the securing gas, commonly argon or carbon dioxide, is not efficiently covering the weld swimming pool, climatic gases like oxygen and nitrogen can contaminate the liquified metal, leading to porosity. In addition, the sanitation of the base products plays a considerable function. Contaminants such as rust, oil, or dampness can vaporize during welding, producing gas pockets within the weld. Welding parameters, consisting of voltage, present, take a trip rate, and electrode type, additionally influence porosity formation. Utilizing improper settings can create extreme spatter or warmth input, which subsequently can lead to porosity. Additionally, these details the welding strategy employed, such as gas steel arc welding (GMAW) or shielded steel arc welding (SMAW), can influence porosity formation as a result of variations in warmth distribution and gas insurance coverage. Understanding and controlling these elements are essential for lessening porosity in welding procedures.
Impacts of Porosity on Weld Top Quality
The visibility of porosity likewise compromises the weld's resistance to rust, as the entraped air or gases within the gaps can respond with the surrounding setting, leading to destruction over time. In addition, porosity can hinder the weld's capacity to endure pressure or influence, additional jeopardizing the total high quality and reliability of the bonded structure. In crucial applications such as aerospace, automotive, or architectural constructions, where safety and security and longevity are vital, the detrimental results of porosity on weld high quality can have extreme repercussions, emphasizing the relevance of lessening porosity via appropriate welding techniques and treatments.
Techniques to Decrease Porosity
Furthermore, utilizing the ideal the original source welding parameters, such as the appropriate voltage, present, and take a trip rate, is crucial in avoiding porosity. Preserving a constant arc size and angle throughout welding additionally aids reduce the possibility of porosity.

Moreover, picking the appropriate securing gas and maintaining proper gas flow rates are important in reducing porosity. Utilizing the suitable welding method, such as back-stepping or utilizing a weaving movement, can likewise assist disperse warm uniformly and minimize the possibilities of porosity formation. Finally, guaranteeing appropriate ventilation in the welding environment to remove any potential resources of contamination is essential for attaining porosity-free welds. By carrying out these techniques, welders can successfully decrease porosity and generate top notch welded joints.
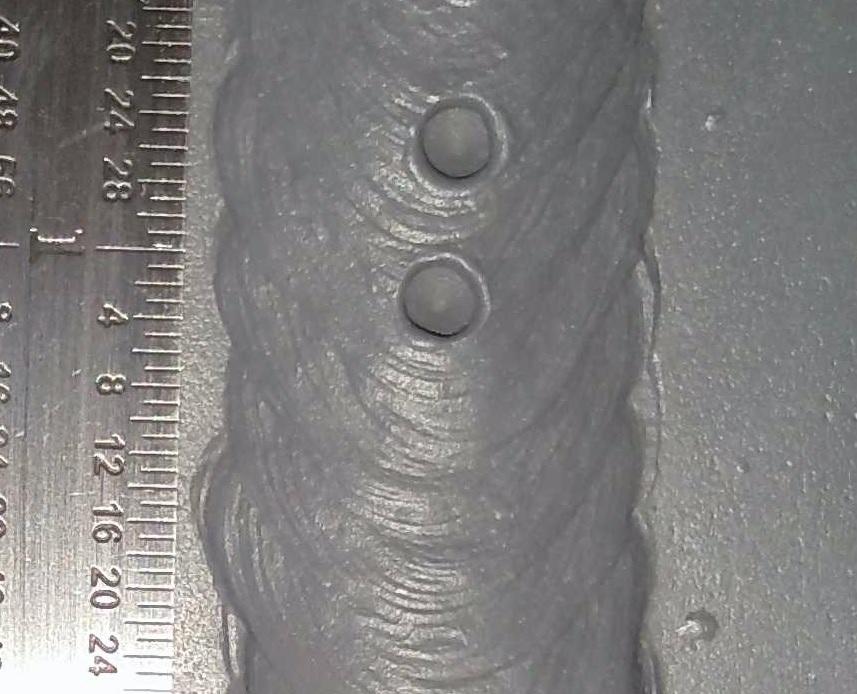
Advanced Solutions for Porosity Control
Implementing cutting-edge modern technologies and cutting-edge techniques plays a critical duty in accomplishing superior control over porosity in welding procedures. One sophisticated solution is using innovative gas blends. Protecting gases like helium or a mixture of argon and hydrogen can aid minimize porosity by supplying better arc security and boosted gas protection. In addition, utilizing advanced welding strategies such as pulsed MIG welding or customized atmosphere welding can additionally assist reduce porosity concerns.
An additional sophisticated remedy includes making use of advanced welding tools. For instance, using equipment with integrated attributes like waveform control and sophisticated power resources can enhance weld high quality and reduce porosity dangers. Additionally, the execution of automated welding systems with precise control over specifications can dramatically minimize porosity flaws.
Moreover, including advanced tracking and assessment modern technologies such as real-time X-ray imaging or automated ultrasonic screening can aid in discovering porosity early in the welding procedure, permitting for immediate corrective actions. Generally, incorporating these innovative remedies can greatly improve porosity control and improve the general high quality of bonded parts.
Verdict
To conclude, recognizing the scientific research behind porosity in welding is essential for welders and producers to create high-grade welds. By recognizing check over here the variables affecting porosity development and applying strategies to decrease it, welders can boost the total weld top quality. Advanced remedies for porosity control can better boost the welding procedure and make sure a strong and reputable weld. It is necessary for welders to constantly inform themselves on porosity and carry out best techniques to achieve optimal results.